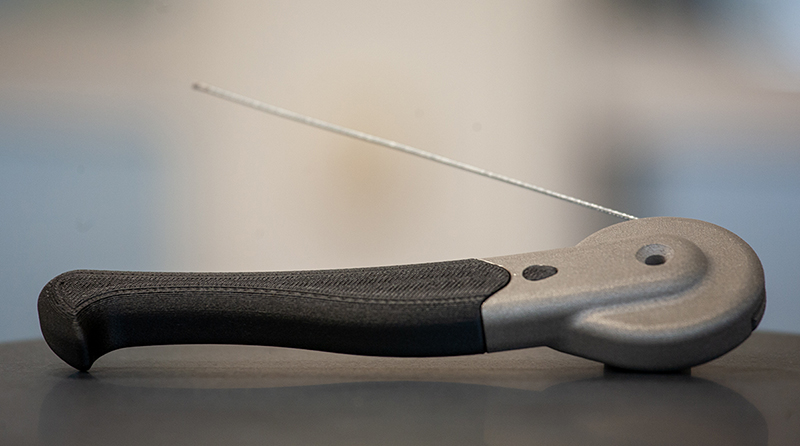
Et projekt om et håndtag, fra designskitse til et fuldt funktionsdygtigt produkt ved hjælp af additiv fremstilling. Ved at bruge additiv fremstilling og innovativt design er resultatet produkter, der vejer mindre og koster mindre at producere.
For et stykke tid siden fik Protech et spørgsmål fra en af sine partnere: Kan man konstruere et håndtag ud fra en designskitse? Håndtaget skulle først produceres som en prototype og senere i en mindre mængde på fem håndtag. Den endelige mængde producerede håndtag ville være 100 stykker om året. Håndtaget skulle være let, og derfor blev aluminium foreslået.
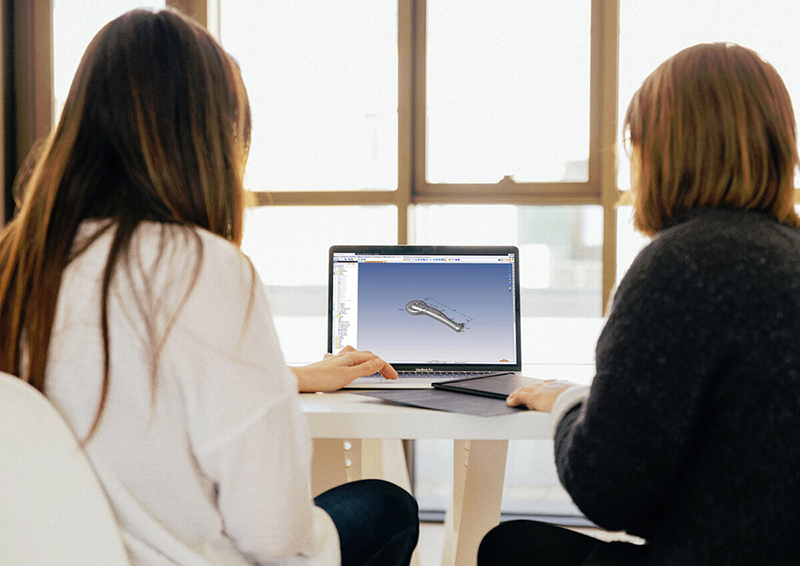
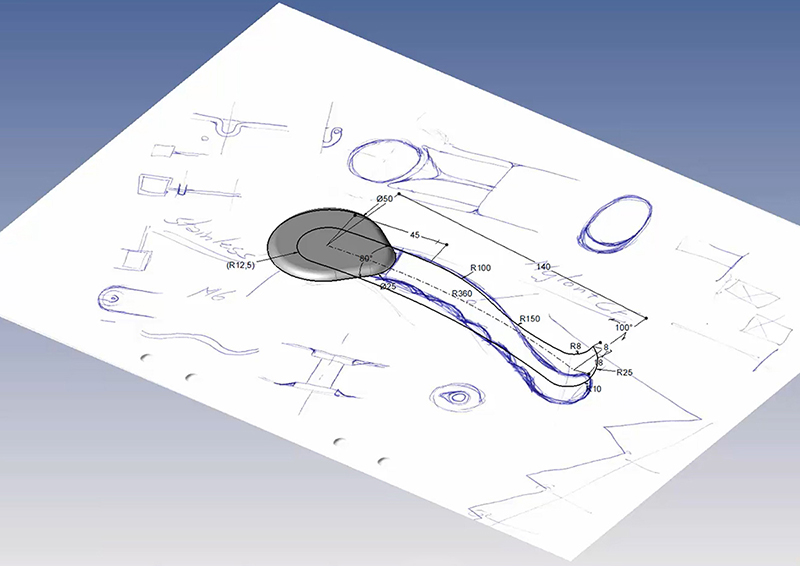

Fræset håndtag i aluminium
Vores partner ønskede, at håndtaget skulle have en glat overflade for at lette rengøringen. Dette krav betød, at vi ikke kunne gøre produktet let med ribber og huller udefra på håndtagets overflade. Det første design tog 12 timer fra skitse til færdig CAD-fil og blev udført i det integrerede CAD/CAM-systemet TopSolid’Design. Da designet var færdigt, lavede vi CNC-programmeringen i TopSolid’Cam og begyndte bearbejdningen. Det færdige håndtag blev rigtig godt, men krævede en masse manuelt arbejde. Vi fjernede håndtaget fra fræseblokken, rettede overfladerne til og sandblæste derefter hele overfladen. Det færdige håndtag vejede 187,5 gram.
Fræsetiden for det første håndtag var ret lang. Det er forventeligt, når man fræser en første prototype, da der ofte er brug for en masse værktøjsopstilling og omprogrammering af NC-koden, før maskinoperatøren er helt tilfreds. Den første fræsning tog 8 timer, og omkostningerne inklusive materialer, CNC-programmering og maskintid var 807 euro. Den næste fræsning af et håndtag tog 1 time og 25 minutter, og der var bestemt meget mere at gøre for at nedbringe den tid i maskinen. I tabellen nedenfor kan du se omkostningerne og produktionstiden for nogle forskellige produktionsmængder.
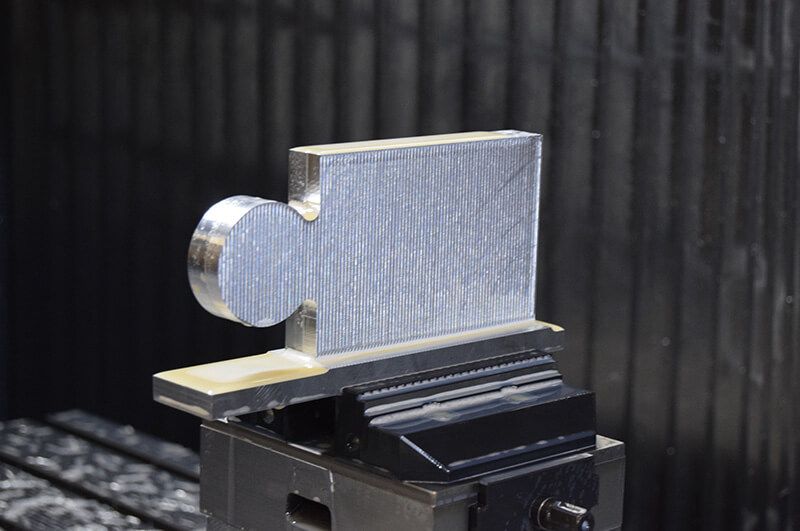
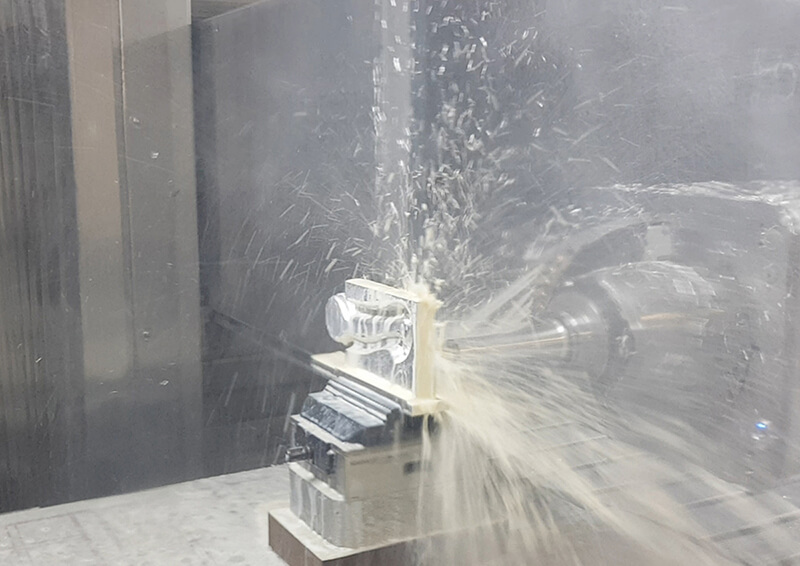
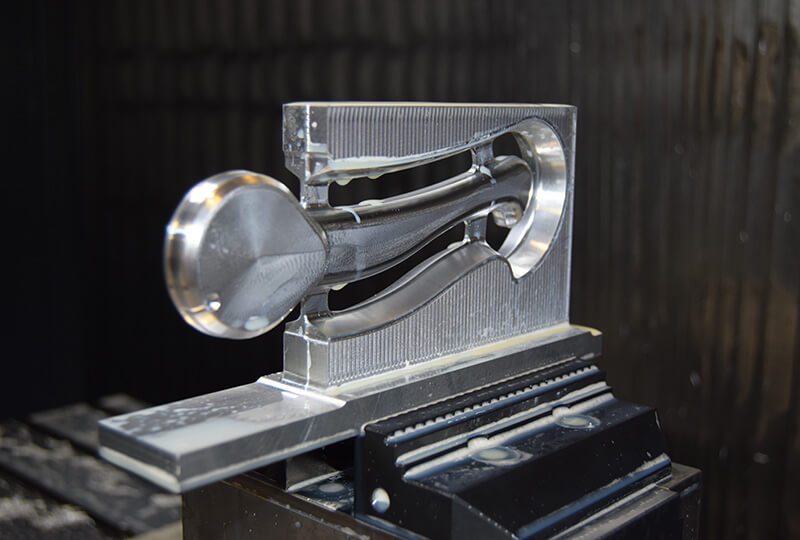
Hvorfor ikke bruge additiv fremstilling?
Efter at have analyseret vægten og produktionsomkostningerne ved det fræsede aluminiumshåndtag spurgte vi os selv – hvorfor ikke bruge additiv fremstilling og producere et hult håndtag i rustfrit stål? Kravene til håndtaget var, at håndtagets fastgørelsesdel skulle være i metal, men ikke nødvendigvis i aluminium.
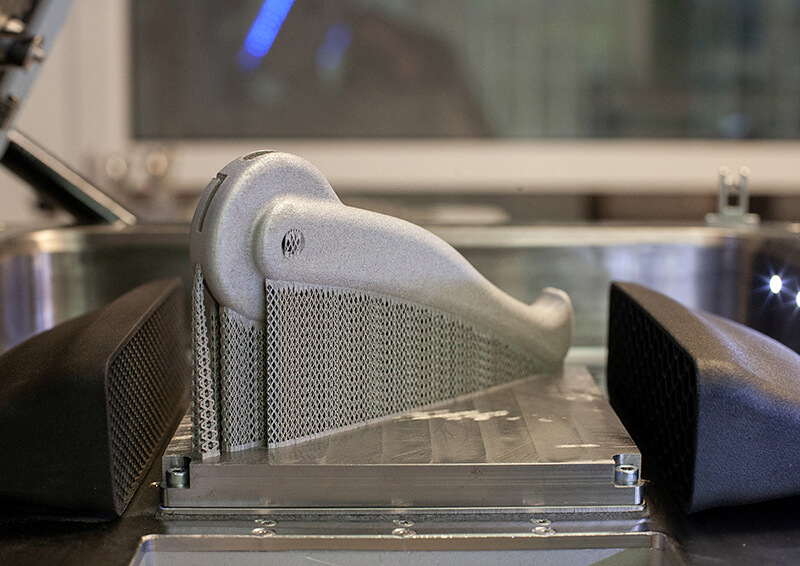
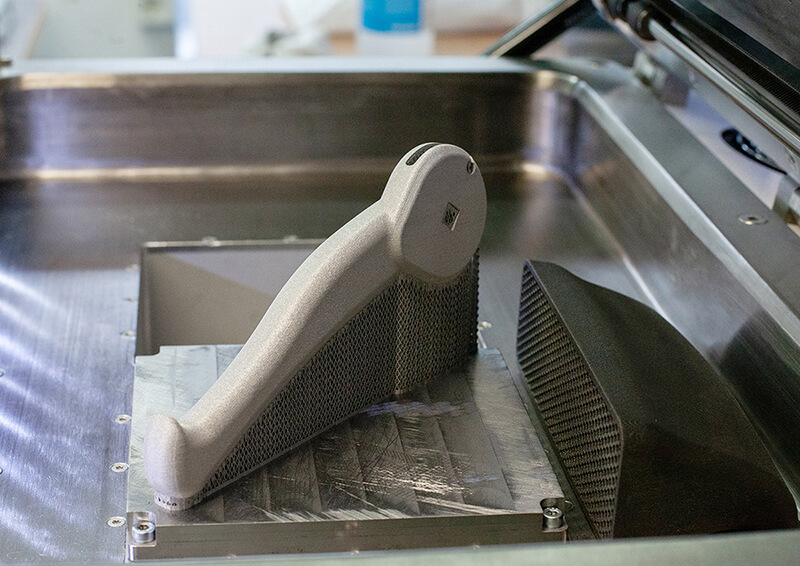
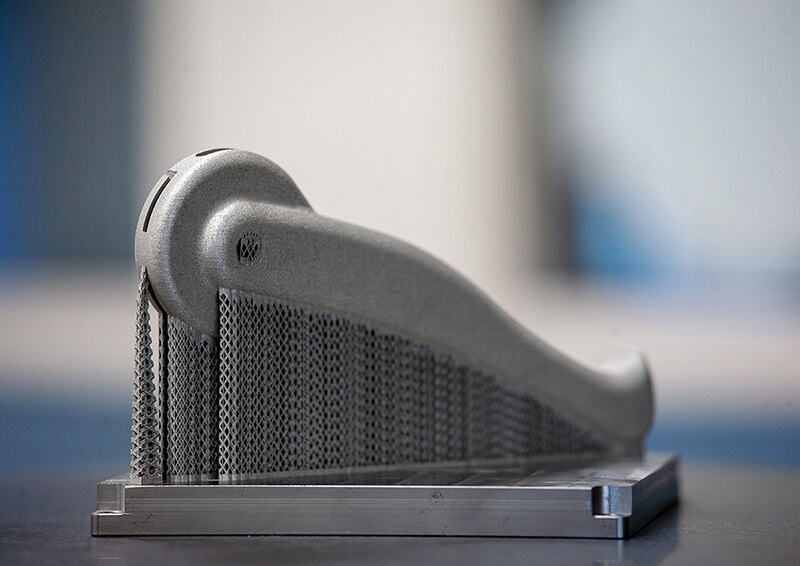
Vi valgte at fremstille det hule håndtag i rustfrit stål (316L) i stedet for aluminium, da maskinomkostningerne til produktion med additiv fremstilling er betydeligt lavere i rustfrit stål end i aluminium. Tilgængeligheden af produktionskapacitet til additiv fremstilling i rustfrit stål er også betydeligt højere end i aluminium. Det oprindelige håndtagsdesign blev lavet hult med en materialetykkelse på 1 mm. Vi tilføjede også et lille hul for at få overskydende pulver ud af håndtaget. Det tog mindre end 5 minutter i CAD-systemet at foretage de to justeringer. For at kunne 3D-printe et komplet håndtag var vi nødt til at tilføje en støttestruktur. Generering af støttestrukturen er en relativt automatisk proces. Det tog 15 minutter at generere støttestrukturen til det komplette håndtag. Det tog 43 timer og 11 minutter at printe det hule håndtag i vores Xact Metal XM200C. XM200C’s byggevolumen begrænsede os til at printe et håndtag ad gangen.
Fjernelse af støttestrukturen efter 3D-printning med Metal Powder Bed Fusion (Metal-PBF) er i mange tilfælde et tidskrævende arbejde. For en detalje, der ligner vores håndtag, sker fjernelsen i de fleste tilfælde manuelt. 3D-printningen af det hule håndtag gik rigtig godt og med en vægt på 112,2 gram. Håndtagets vægt var tæt på målet på under 100 gram, men omkostningerne pr. håndtag var for høje, og produktiviteten var for dårlig. Selv om der blev brugt en maskine med et større byggeområde, og flere detaljer kunne printes samtidig, var produktiviteten for lav.
Kulfiberforstærket nylon giver styrke til håndtaget
Udfordringen var at reducere håndtagets vægt uden at gå på kompromis med designkravene. Håndtagets fastgørelsesdel skulle være af metal, men hvad sker der, hvis man kombinerer plast og metal? Med et todelt design kunne håndtagsdelen laves af plastik, hvilket drastisk reducerede vægten af hele håndtaget. Det tog 8 timer at ombygge håndtaget til et todelt produkt.
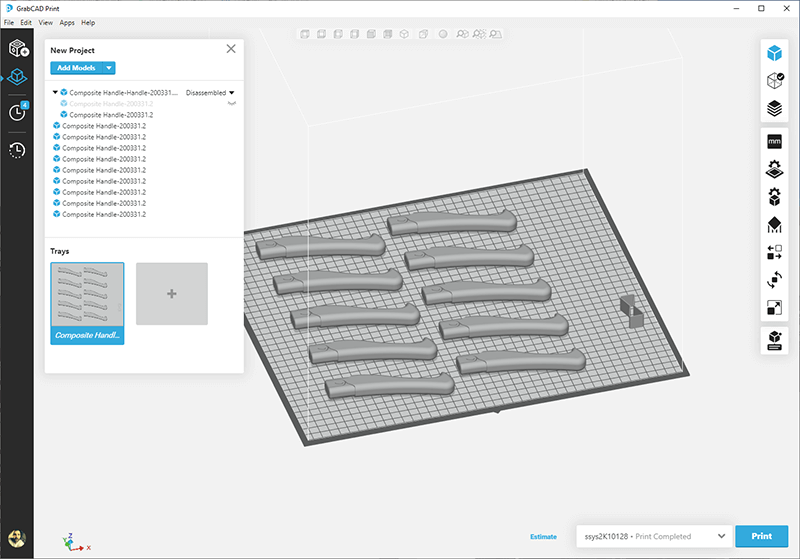
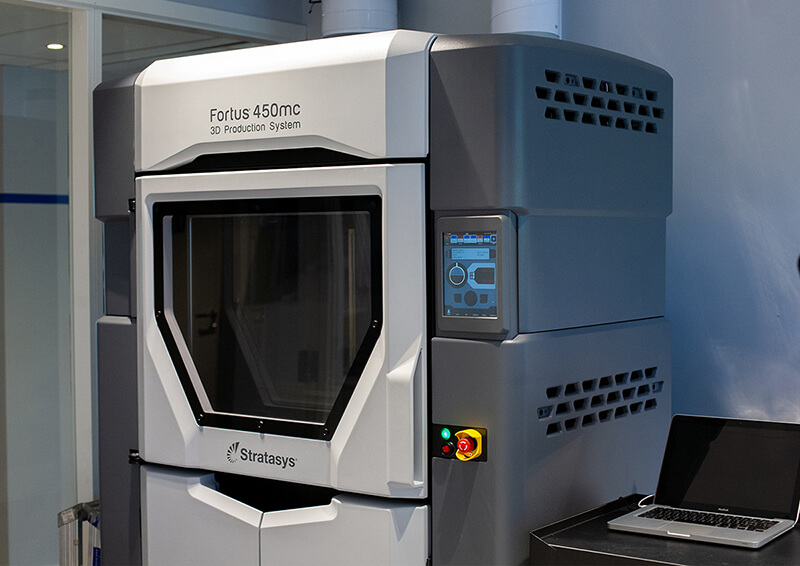
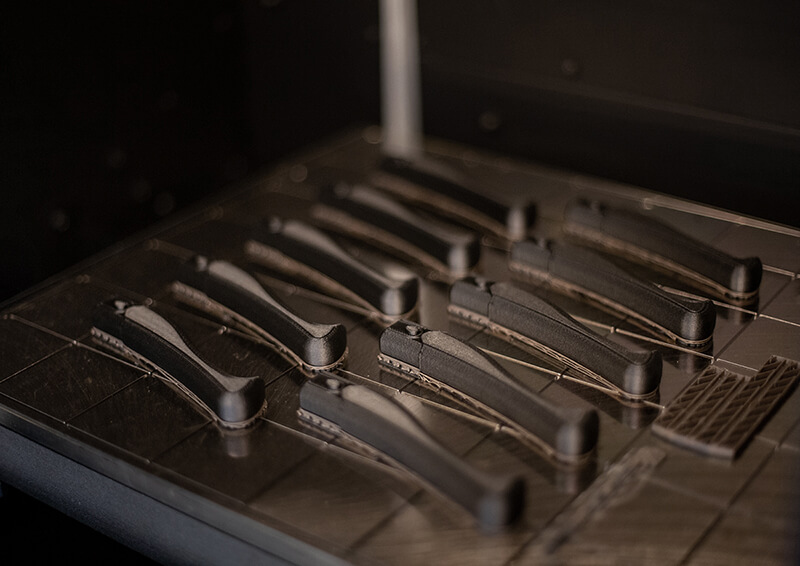
Håndtagsdelen af det todelte håndtag blev designet til at blive 3D-printet i kulfiberforstærket nylon (Nylon 12CF) på vores Stratasys 450mc 3D-printer. Materialets mekaniske egenskaber er fremragende, og delen kunne printes med en indvendig gitterstruktur. Ti håndtagsdele blev fordelt på 3D-printerens byggeflade og printet på 7 timer og 36 minutter. En enkelt håndtagsdel tog 1 time og 10 minutter at printe og havde en samlet vægt på 25 gram.
Fastgørelsesdelen er printet i Xact Metal
Håndtagets fastgørelsesdel blev designet til at reducere printtiden og behovet for en støttestruktur. Ti fastgørelsesdele kunne pakkes på byggeplatformen på vores Xact Metal XM200C og tog 125 timer og 10 minutter at printe. Men det tog tid at fjerne støttestrukturen og færdiggøre hver enkelt del. Hver del blev derefter sandblæst for at opnå en glat overfladestruktur. En fastgørelsesdel tog 17 timer at printe og vejede 60 gram.
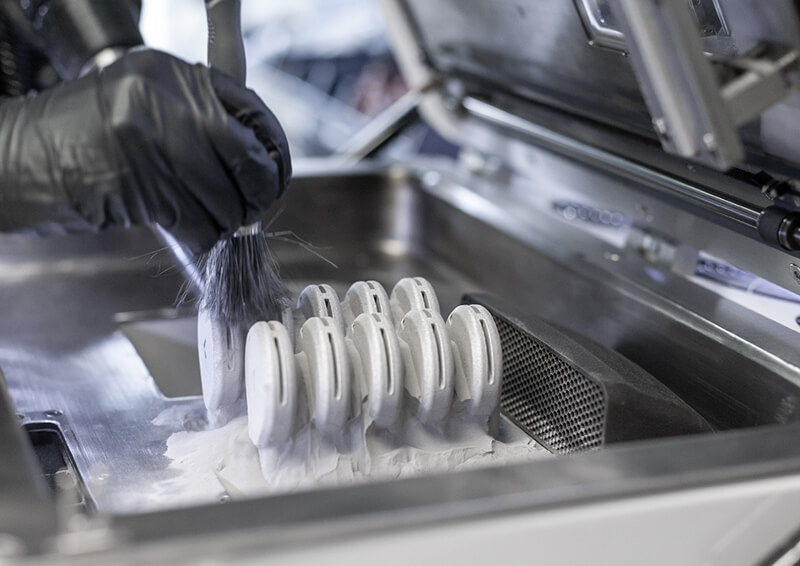
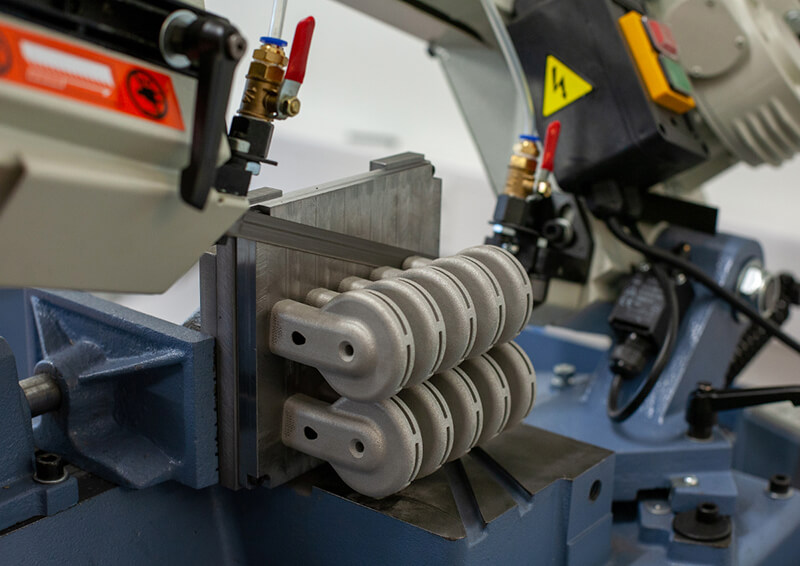

Et komplet håndtag vejer 85 gram
Det todelte håndtag endte med en samlet vægt på 85 gram, hvilket betød den laveste vægt og de laveste produktionsomkostninger af alle de håndtagsvarianter, der blev produceret i projektet.
Brug af additiv fremstilling og innovativt design resulterer i produkter, der vejer mindre og koster mindre at producere. Additiv fremstillingsdesign udfordrer designere til at tænke ud af boksen, men kan resultere i bedre produkter end traditionelle fremstillingsteknikker – tænk additiv fremstilling.
Oversigt over omkostninger
Tabel, der viser omkostninger og tid til at producere 1, 10, 25 og 100 af de forskellige håndtagsvarianter.
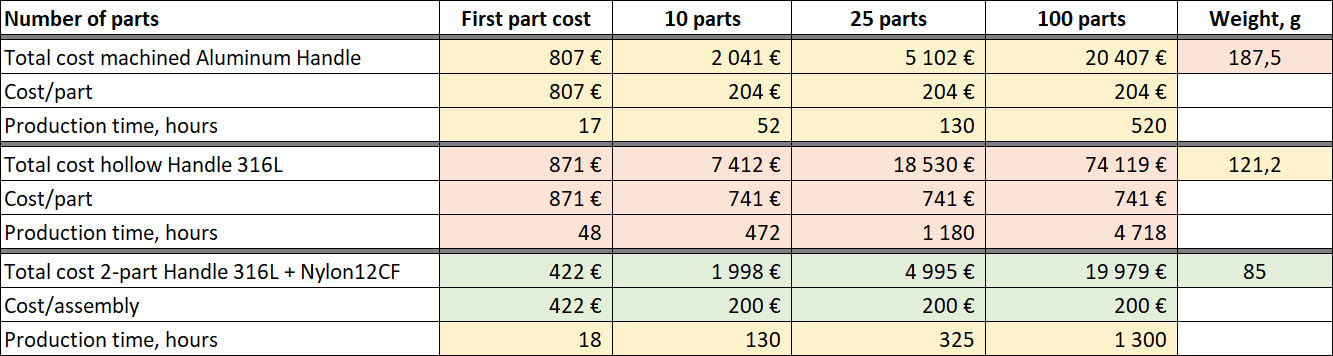
Omkostningerne i tabellen er de faktiske omkostninger i Sverige. Beregningen af produktionsomkostningerne varierer naturligvis fra land til land. Manuel arbejdskraft udgør en stor del af omkostningerne ved de forskellige varianter af håndtagskonstruktion, og omkostningerne til manuel arbejdskraft varierer meget fra land til land. Tabellen viser omkostninger og ikke den faktiske pris på et fremstillet håndtag. Virksomheder, der fremstiller produkter, lægger altid en margin til deres produktionsomkostninger. Margenen varierer meget fra virksomhed til virksomhed. Derfor kan den faktiske pris på et produkt variere meget.
Alle de konklusioner, der er draget i dette projekt, er helt geometriafhængige. Et andet produkt med et andet design vil sandsynligvis resultere i andre konklusioner.
Protech har fået tilladelse til at offentliggøre dette projekt for at inspirere andre til at overveje, hvordan deres produkter fremstilles. Projektet kan bruges frit, og modeller og underliggende beregningsdata kan rekvireres fra Anders Brask (kontaktoplysninger nederst).
Når man reducerer et produkts vægt, sparer man omkostninger, reducerer produktets CO2-fodaftryk og transportomkostningerne. Additiv fremstilling vil spille en vigtig rolle i ændringen af den måde, produkter fremstilles på.
Kontakta en av våra säljare för mer information
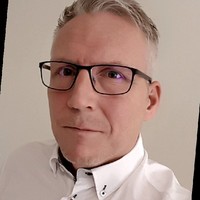