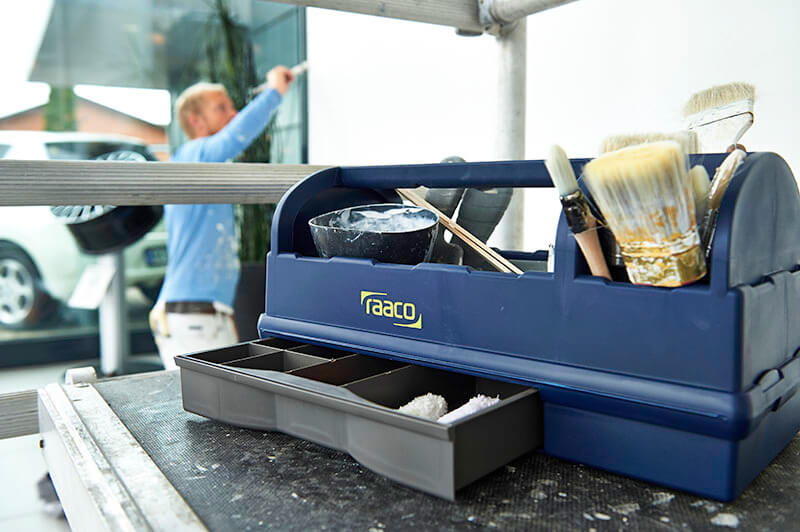
Raaco har i fem år anvendt deres Stratasys 3D-printer til udviklingsprojekter, men i de seneste seks måneder fylder produktionsværktøjer mere og mere – særligt i det nye kulfiberfyldte ABS-CF10 materiale.
Raaco har siden 1956 udviklet og fremstillet innovative og pladsbesparende opbevaringsløsninger til både industrien og professionelle håndværkere verden over. Raaco designer og producerer i Nykøbing Falster, hvor der skabes orden i alt fra helt små virksomheder til Airbus Group. I 2014 får en specifik produktforespørgsel Raaco at investere i deres første 3D-printer, en brugt Dimension 1200ES SST, og i 2017 blev den opdateret til den nuværende model, en Stratasys F170.
Kulfiberfyldt ABS som optimeret produktionsværktøj
I 2017 opgraderede Raaco til deres nuværende F170 fra Stratasys. Selvom printeren ligesom sin forgænger fortsat er tænkt som et udviklingsværktøj er den de seneste 6 måneder overvejende blevet brugt til produktionsværktøjer. Blandt andet bliver der produceret robotgribere med indbyggede vakuum-kanaler til sugekopper, i materialet ABS-CF10 – et materiale som er både stærkere og stivere end det ASA-material Raaco anvender til prototyper i hverdagen.
3D-printning af gribere forenkler geometrien og reducerer vægten af produktionshjælpen, hvilket reducerer belastningen på robotten eller gør det muligt at bruge en mindre og billigere robot til opgaven.
— Tore Hermansen, Product Design Manager på Raaco.
Ud over produktionshjælpemidler har Raaco erfaret, at en prototype, der er så tæt på det færdige produkt, har en række yderligere fordele, nemlig at de 3D-printede prototyper også kan bruges til at bygge produktionslinjer.
Fra indkøring af robotter, finjustering af grafiske prints og sikring af, at samlingen af delkomponenter undervejs er optimal – ved at bruge prototypen som model for disse opsætninger er vi et skridt foran, når vi har den færdige form.
— Tore Hermansen, Product Design Manager på Raaco.
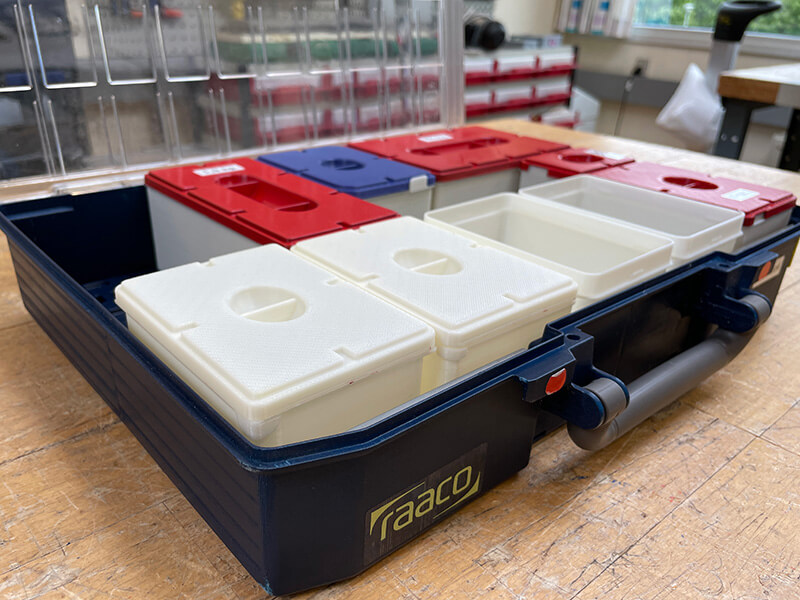
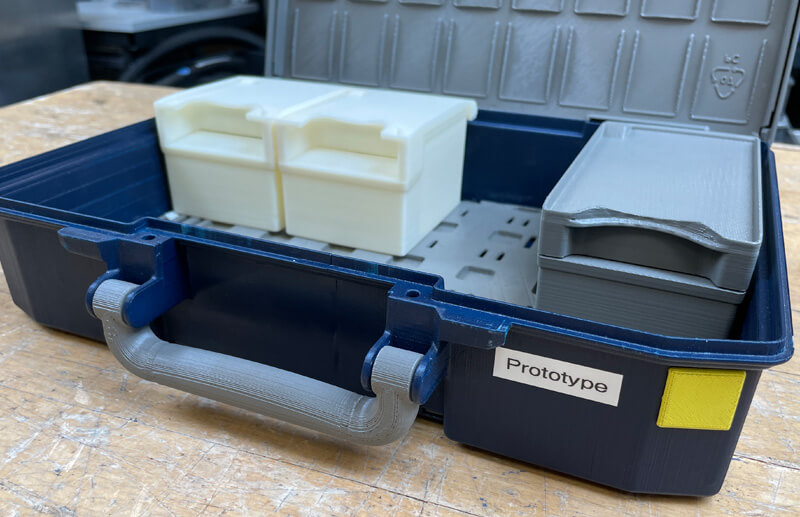
Funktionsdygtige prototyper med additiv fremstilling
Siden indkøbet af den først 3D-printer, er den blevet en fast del af produktudviklingen. Teknologien tillader flere justeringer undervejs i processen da nye revisioner kan produceres hurtigt og præcist, så uanset om der udvikles nye sortimentsæsker eller opbevaringssystemer, maler og limer Raaco deres prototyper efter behov, så de fremstår nærmest identiske med det færdigproducerede. Herefter laves funktionstest med de 3D-printede modeller så både ergonomi og funktion er afprøvet og godkendt inden den endelige produktionsform bestilles.
Før i tiden lavede vi et eller to forsøg, før vi lavede en form til et nyudviklet produkt, men i dag laver vi ofte fem eller seks korrektioner, hvilket sparer os for dyre og tidskrævende korrektioner af den endelige form.
— Tore Hermansen, Product Design Manager på Raaco.
Nogle gange bruger Raaco endda prototypen til markedsføringsmateriale, så de har mulighed for at promovere produkter, selv før den første del er blevet støbt. Alt dette er muligt, fordi den 3D-printede prototype er stort set identisk med det endelige produkt.
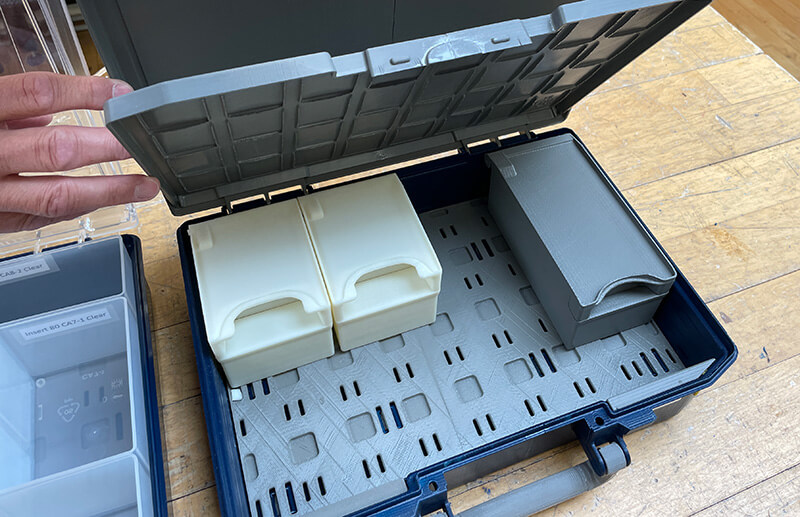
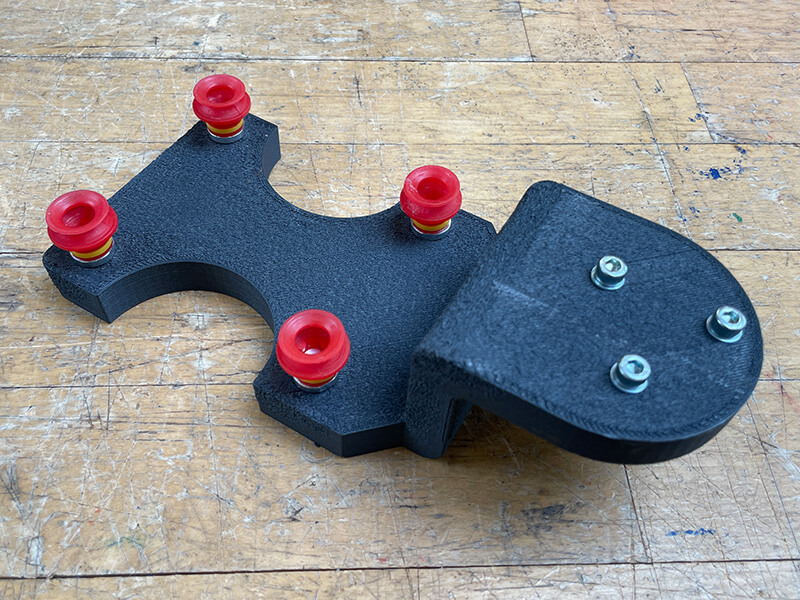
3D-print optimerer hele produktudviklingsfasen
Raaco investerer i deres første 3D-printer da Airbus i 2014 efterspørger sortimentsæsker med blandt andet et klik-system som fikserer indsatsene til bunden, noget man hidtil havde en modelsnedker til at konstruere prototyper til. Denne tidskrævende proces består i manuelt at skære, forme og lime plast-stykker sammen.
Med behov for at konstruere en serie sortimentsæsker hvor funktion og udseende ligger så tæt på færdigt produkt som muligt, samt inkludere et klik-system med det rigtige feedback, beslutter Raaco at investere i en 3D-printer. Valget var en Dimension SST 1200ES 3D-printer, som efter 3 måneders nonstop print leveret prototyper til godkendelse, bestående af komplette 3D-printede æsker hvor både håndtag, låg og indsatse med fungerende klik-system er funktionelt og visuelt, så tætte på det færdige produkt som ønsket.
Med 3D-print kan vi se et påtænkt produkt med vores hænder, vi kan godkende ergonomien i et håndtag, vi kan teste betjeningselementer og låsefunktioner. Hvis der er behov for justeringer, kan vi nemt revidere produktet, før vi laver den endelige form.
— Tore Hermansen, Product Design Manager på Raaco.
Siden har 3D-print været en fast del af udviklingen hos Raaco og nu også produktionen.
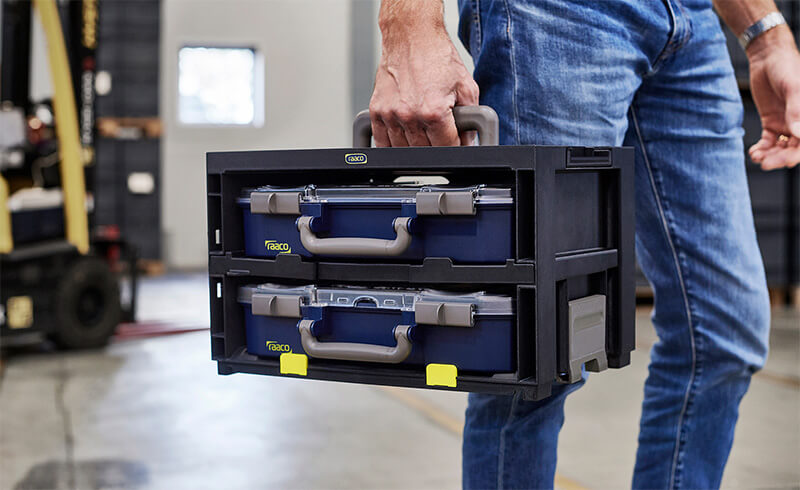
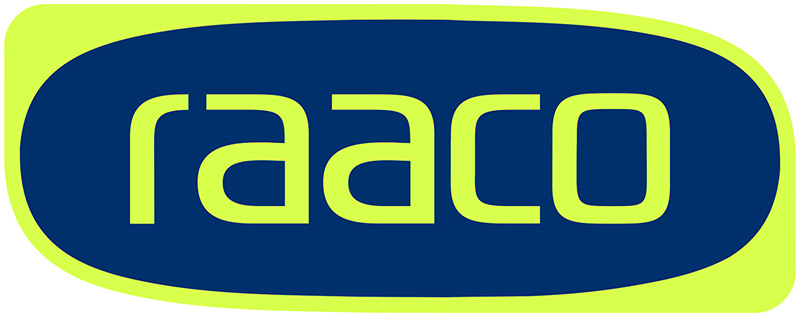